3D Printing
In the Maker Space’s Print Hive students are empowered with a cutting-edge suite of 3D printing technologies, including typical FFF 3D printers, SLS Nylon, DLP resin, and metal 3D printing with Markforged’s Metal X system. This diverse range of technologies allows students to rapidly translate their conceptual designs into tangible prototypes.
3D printing bridges the gap between imagination and reality. By accelerating the prototyping phase, students can quickly assess the feasibility of their ideas and make necessary adjustments before wasting time chasing a flawed design.
Beyond prototyping, the high quality and versatile 3D printing available in the Maker Space allows students to produce end-use parts, creating functional components for various applications. As a process, it offers a valuable step in the design evaluation process, allowing users to scrutinize their designs in real life before committing to more involved subtractive manufacturing using more resilient materials.
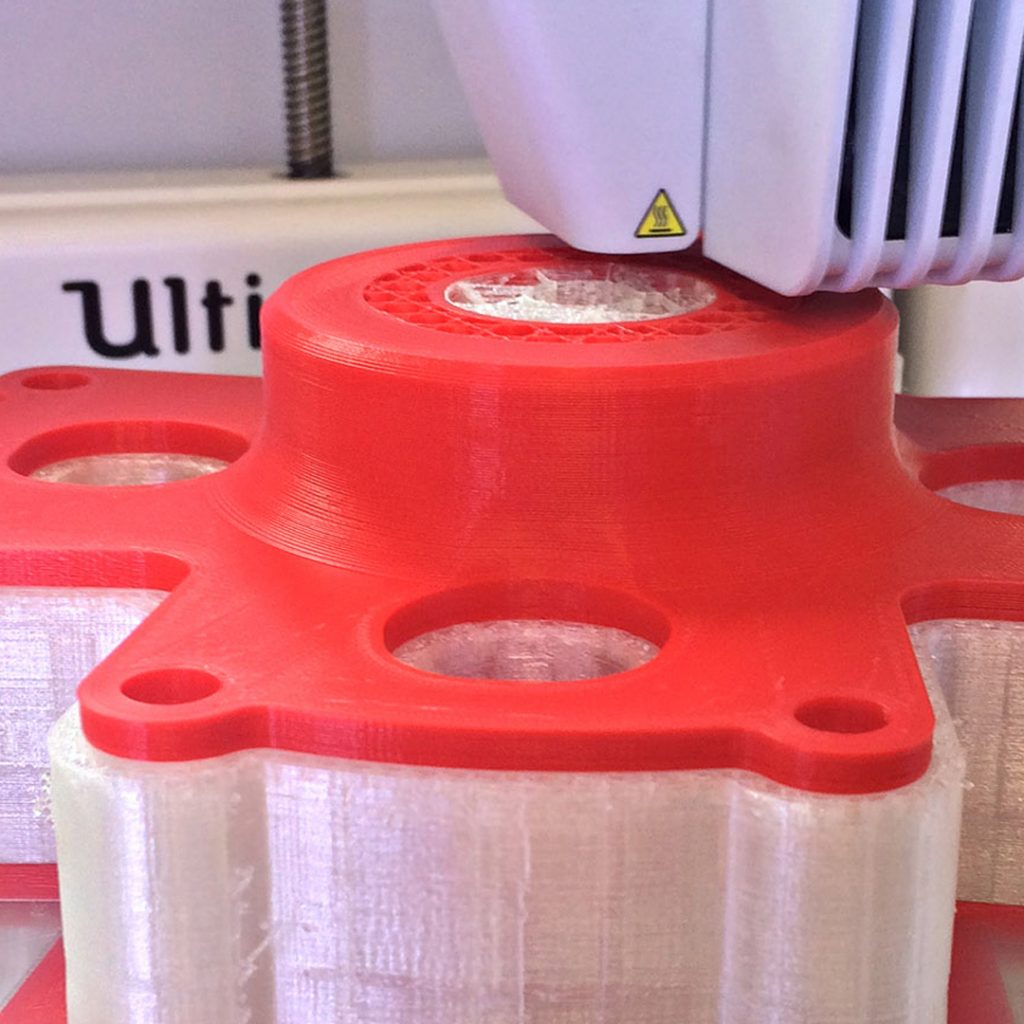
Fused Filament Fabrication
Our range of Ultimaker, Bambu Lab, and Markforged 3D printers allows for quick and inexpensive prototyping using materials like PLA, ABS, and fibre-reinforced nylon.
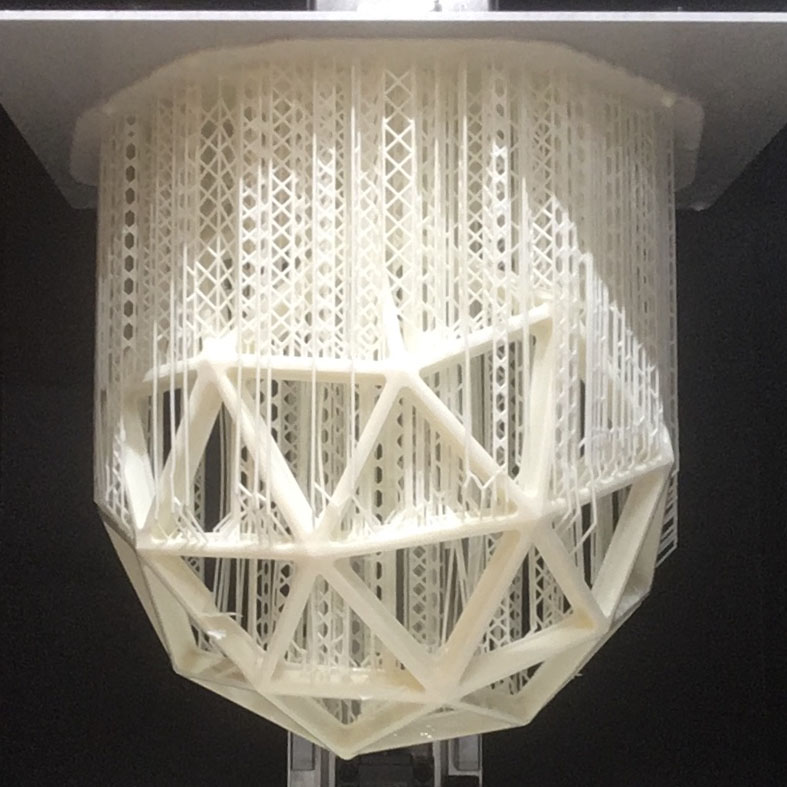
DLP Resin
UV curable resin is selectively hardened by shining high powered UV light through a high-resolution display screen. These printers are capable of producing very high quality prints, with a surface finish almost rivalling injection moulding, and handle fine details for minature models and small scale lab experiments with ease.
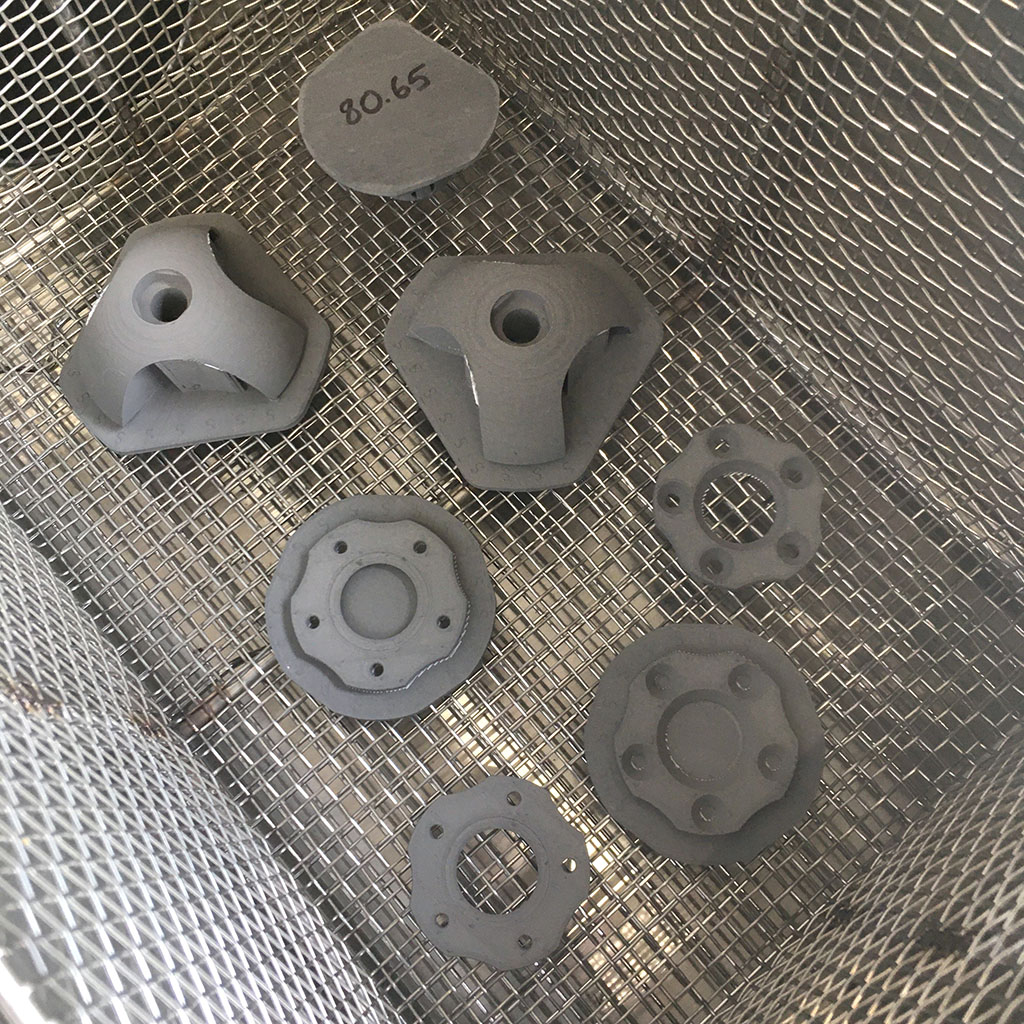
Markforged Metal X
Using Markforged’s fused filament fabrication technology the Metal X system allows printing with a variety of metals, including 17-4PH stainless steel, copper, and exotic super-alloys like Inconel with just a quick sweep out and a nozzle change.
Printed parts are run through a solvent wash and a sintering process to turn them from “green” metal-filled plastic into solid metal components.
SLS Nylon
The Formlabs Fuse prints with nylon powder, using a laser to selectively sinter the powder into a solid form. Because parts being printed are surrounded by unsintered powder there is no need for additional support structures – once the excess material has been cleaned off the parts are finished and ready to use.